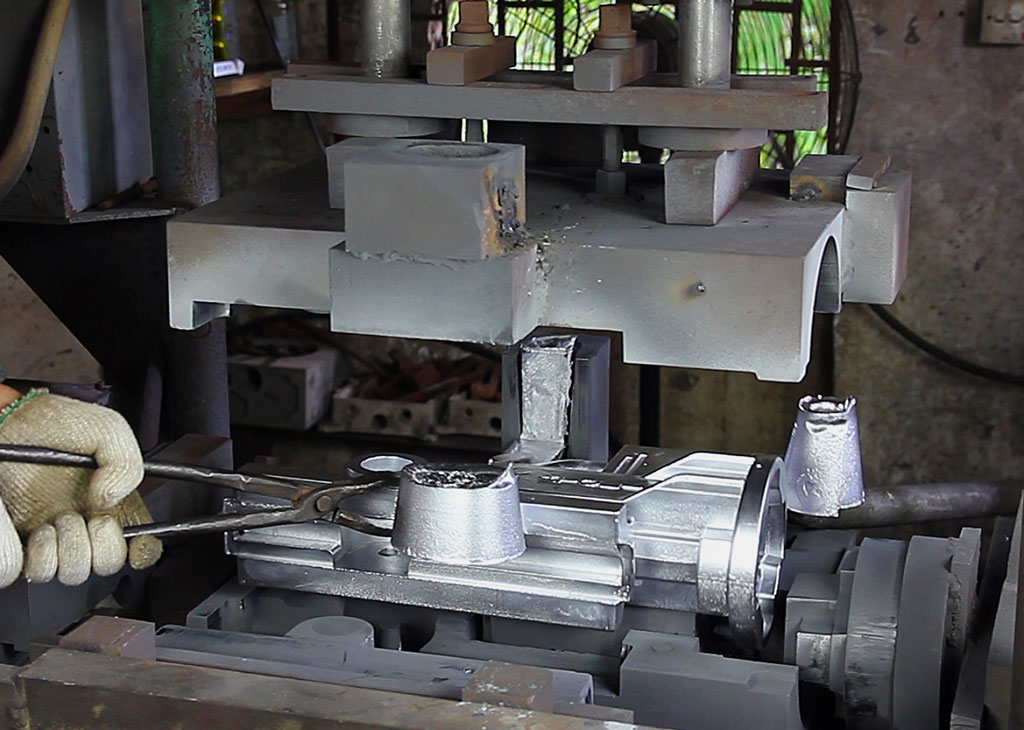
If you're in the manufacturing industry, you must have heard about permanent mold casting or gravity die casting. It's a well-known process that offers many benefits, such as uniformity and improved surface finish. But do you know everything there is to know about it? In this comprehensive guide, we'll take a deep dive into permanent mold casting and explore its advantages, disadvantages, materials used, and how to choose the right company for your needs. So whether you're new to the process or just looking for more information on it, keep reading!
What is permanent mold casting?
Permanent mold casting, also known as gravity die casting, is a manufacturing process that involves pouring molten metal into a reusable mold or die. The mold is made of steel or iron and can be used multiple times to produce identical castings.
Unlike sand casting, which uses sand molds that are destroyed after each use, permanent mold casting offers better surface finish and dimensional accuracy. It's commonly used for high-volume production of small to medium-sized parts such as engine blocks, wheels and gears.
The process begins with the preparation of the mold by coating it with a release agent to prevent the metal from sticking. Then, molten metal is poured into the cavity through gates and runners in the die.
The molten metal solidifies inside the mold and takes its shape. After cooling down and hardening, the part is removed from the mold using ejector pins or other methods.
Permanent mold casting provides consistent results with less waste compared to other processes like sand casting or investment casting.
The benefits of permanent mold casting
Permanent mold casting, also known as gravity die casting, offers numerous benefits over other manufacturing processes. One of the main advantages is its ability to produce complex shapes with high accuracy and surface finish.
Compared to sand casting, permanent mold casting produces parts with a smoother surface finish that requires less post-processing. Additionally, it can achieve thinner wall sections and tighter tolerances which result in less material waste and reduced machining time.
Furthermore, permanent mold casting typically results in stronger and more durable parts due to the improved metallurgical properties resulting from rapid solidification. This makes it ideal for components subjected to heavy loads or extreme temperatures.
Another major advantage of permanent mold casting is its efficiency in producing large quantities of identical parts quickly and cost-effectively. The process allows for repeatable production runs without sacrificing quality or consistency between each part.
Because the molds used in permanent mold casting are made from durable materials such as steel or iron, they have a longer lifespan compared to those used in sandcasting. This translates into fewer tooling costs over time and ultimately lower overall production costs.
The benefits of permanent mold casting make it an attractive option for manufacturers looking for a reliable and efficient method of producing high-quality metal components.
The disadvantages of permanent mold casting
While there are many benefits to permanent mold casting, it's important to also consider the potential disadvantages before deciding if this manufacturing process is right for your needs.
One of the biggest drawbacks of permanent mold casting is that it can be more expensive than other types of casting processes. This is because creating permanent molds requires significant upfront costs for tooling and equipment.
Another challenge with permanent mold casting is that it may not be suitable for all types of materials or designs. For example, complex shapes or thin-walled parts may be difficult to produce using this method. Additionally, certain materials may not flow as easily through a permanent mold as they would in other types of molds.
Permanent molds can also become worn over time, which can affect the quality and consistency of castings produced from them. To address this issue, regular maintenance and repairs may be necessary.
While permanent mold casting typically produces high-quality parts with good surface finishes and dimensional accuracy, it may not always provide the same level of detail or precision as some other manufacturing methods like CNC machining or 3D printing.
While there are certainly some downsides to consider when it comes to permanent mold casting, these limitations can often be mitigated by working with an experienced manufacturer who has a deep understanding of the process and its capabilities.
The types of materials that can be used in permanent mold casting
When it comes to permanent mold casting, there are a variety of materials that can be used. These include metals such as aluminum, brass, and bronze. Each material has its own unique properties and advantages.
Aluminum is one of the most popular materials used in permanent mold casting due to its light weight and high strength-to-weight ratio. It is also highly resistant to corrosion which makes it ideal for use in outdoor applications.
Brass is another common material utilized in permanent mold casting because of its excellent machinability and thermal conductivity. This means that it can easily be shaped into intricate designs while also being able to efficiently transfer heat.
Bronze is yet another option when it comes to selecting materials for permanent mold casting projects. With superior strength and durability, bronze is often chosen for heavy-duty applications such as marine components or machinery parts.
It's important to choose the right material for your project based on factors such as cost, performance requirements, and environmental considerations. A reputable permanent mold casting company will have experience working with a range of different materials and will be able to offer guidance on what would work best for your specific application.
How to choose the right company for your permanent mold casting needs
Choosing the right company for your permanent mold casting needs is a crucial step in ensuring that you receive high-quality products. Here are some tips to help you choose the best company:
1. Experience and Reputation - Look for a company with extensive experience in permanent mold casting and has good reviews from previous clients. This will give you an idea of their work quality, reliability, and customer service.
2. Quality Assurance - Check if the prospective company follows strict quality assurance procedures that ensure consistency in every production run.
3. Materials Used - The type of material used can impact product quality; thus, consider a firm such as those using advanced equipment coupled with skilled personnel to guarantee superior results.
4. Cost-Efficiency- Always strive for cost-effective solutions suitable for your budget without compromising on quality standards.
5. Turnaround Time - Choose a firm capable of meeting tight deadlines while still maintaining exceptional standards throughout production cycles
By considering these factors when choosing which manufacturer to work with, you'll be sure to get superior products at competitive prices while enjoying seamless processes from start to finish
Conclusion
To sum up, permanent mold casting is an excellent choice for producing high-quality, accurate, and consistent metal parts. It provides numerous advantages over other casting methods and can be used with a wide range of materials.
Whether you need to create complex shapes or simply produce large quantities of identical parts, permanent mold casting is worth considering. By choosing the right company to work with and using the appropriate techniques and materials, you can achieve outstanding results that meet your unique needs.
So if you're looking for a reliable way to manufacture metal components in large quantities at an affordable cost without sacrificing quality - consider permanent mold casting today!