Plastic injection molding is a widely used manufacturing process that involves injecting molten plastic material into a mold cavity under high pressure. This versatile technique is employed in various industries to produce a vast array of plastic parts and products, ranging from intricate components to everyday items. By mastering the art of plastic injection molding, manufacturers can efficiently create precise, high-quality plastic components that meet the demands of modern production requirements. Understanding quick turn injection molding of this process is essential for achieving optimal results and maximizing production efficiency.
Types of Plastic Used
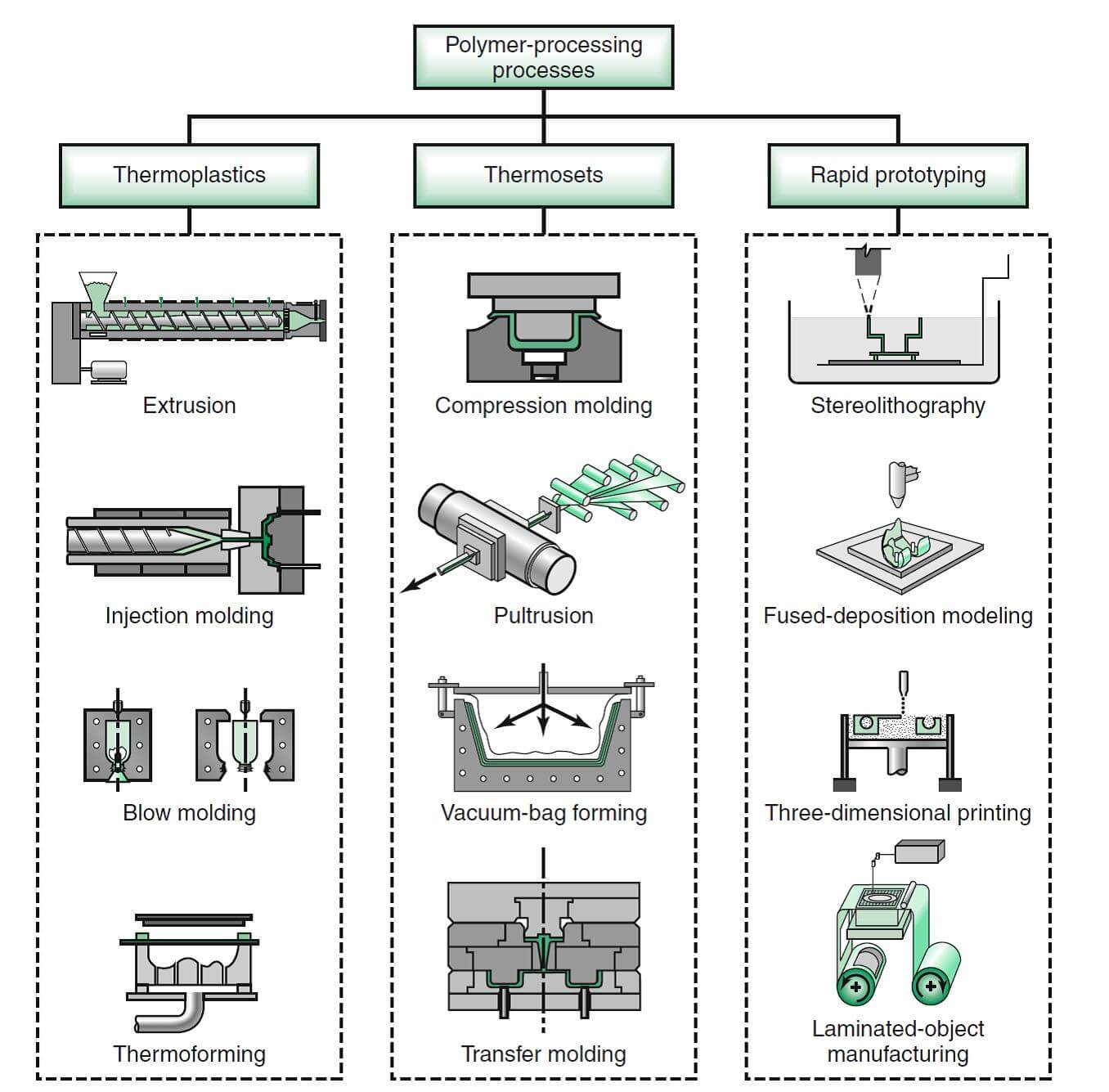
Plastic injection molding can accommodate a variety of materials, each with unique properties and advantages. Some common types of plastics used in the process include thermoplastics, thermosets, and elastomers.
Thermoplastics are the most commonly used plastics in injection molding due to their ability to be easily melted and reshaped multiple times. Examples of thermoplastics include polyethylene, polypropylene, and polystyrene.
Thermoset plastics, on the other hand, are hardened and set during the molding process, making them more rigid and heat-resistant. Materials such as epoxy and phenolic resins fall under this category and are commonly used for specific applications that require high durability.
Steps in Plastic Injection Molding
To begin the plastic injection molding process, raw materials are carefully selected and prepared. These materials are then heated until they reach a molten state. Once in this liquid form, the plastic is ready to be injected into the mold cavity.
The next step involves injecting the molten plastic material into the mold cavity under high pressure. This pressure ensures that the material fills the cavity completely, taking on the precise shape of the mold. After the material is injected, it is left to cool and solidify within the mold.
Common Defects and Remedies
When carrying out plastic injection molding, it's essential to be aware of common defects that can arise during the process. One such issue is known as "short shot," where the molten plastic does not completely fill the mold cavity. To remedy this, adjusting the injection speed or increasing the melt temperature can help achieve a more complete fill.
Another common defect to watch out for is "burn marks," which are visible discolorations on the final product caused by excessive heat. To address this problem, lowering the mold temperature or reducing the injection speed can help prevent the plastic from overheating and resulting in burn marks.
Lastly, "warpage" is a defect where the molded part becomes distorted or twisted. This can happen due to uneven cooling or excessive internal stress within the plastic. To combat warpage, ensuring uniform cooling of the mold and choosing the appropriate type of plastic material with lower shrinkage properties can help minimize this issue.