Plastic injection molding is a widely-used manufacturing process that involves injecting molten plastic material into a mold cavity. quick turn injection molding allows manufacturers to produce a wide variety of plastic products, ranging from small components to large automotive parts. The versatility and efficiency of plastic injection molding make it a popular choice for industries such as automotive, electronics, packaging, and healthcare.
The process of plastic injection molding begins with the design of a mold, which determines the shape and features of the final product. Once the mold is created, plastic material is heated to a high temperature and injected into the mold cavity under high pressure. The material then cools and solidifies, taking the shape of the mold. The finished product is ejected from the mold, ready for further processing or assembly. Plastic injection molding offers precision, repeatability, and cost-effectiveness, making it an essential technique for modern manufacturing.
Types of Injection Molding Processes
When it comes to plastic injection molding, there are several types of processes that are commonly used in the industry. Each process brings its own advantages and is chosen based on the specific requirements of the project.
Conventional Injection Molding: This is the most common type of injection molding process. It involves injecting molten plastic material into a mold cavity, where it cools and solidifies to form the desired part or product. Conventional injection molding is versatile and cost-effective, making it a popular choice for a wide range of applications.
Insert Molding: In insert molding, pre-formed components are placed into the mold cavity before the plastic material is injected. This process allows for combining multiple materials or components into a single part, streamlining production and enhancing product performance.
Multi-Shot Injection Molding: Multi-shot molding enables the injection of multiple materials or colors into the same mold in separate shots. This process is utilized to create complex parts with varying properties or aesthetics, increasing design flexibility and reducing the need for secondary assembly processes.
Key Components of Injection Molding Machines
In injection molding, machines are comprised of several key components that work together seamlessly to produce high-quality plastic parts. The injection unit is responsible for melting and injecting the plastic material into the mold. It consists of the hopper, barrel, screw, and heater bands that work in harmony to melt and mix the resin thoroughly before injection.
Next, the clamping unit holds the two halves of the mold together under pressure during the injection and cooling phases. This unit is essential for maintaining the mold's integrity and ensuring precise and consistent part dimensions. It consists of the clamping mechanism, mold cavity, and ejection system that work together to create the final product.
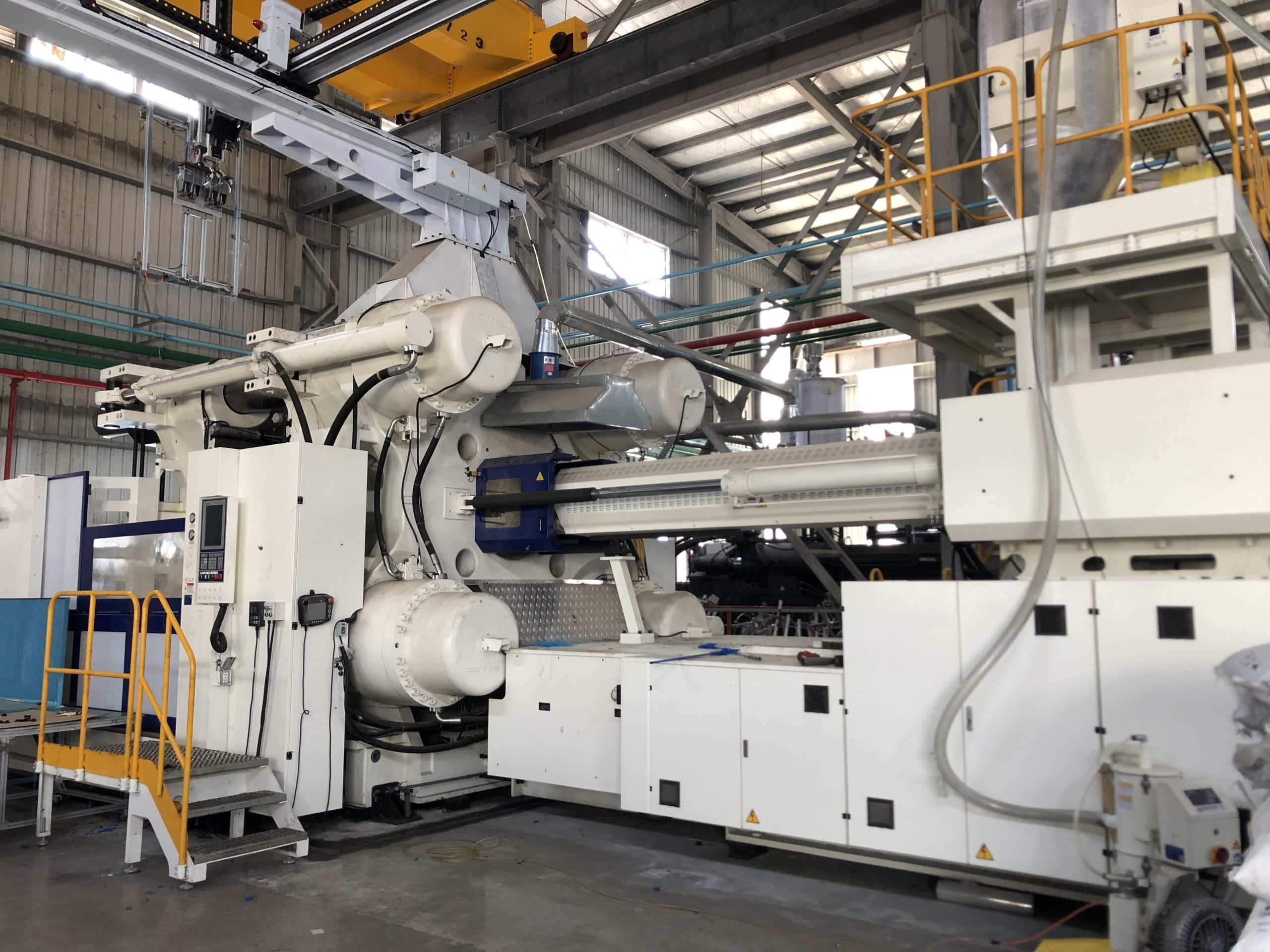
The control system of an injection molding machine is the brains behind the operation, overseeing all the machine's functions and settings. It regulates factors such as injection pressure, temperature, and cycle time to ensure the manufacturing process runs smoothly and efficiently. A well-calibrated control system is crucial for achieving optimal results in plastic injection molding.
Common Challenges Faced in Injection Molding
One common challenge encountered in plastic injection molding is achieving consistent quality in the finished products. Maintaining uniformity in dimensions, surface finish, and overall appearance across a large production run can be a demanding task.
Another significant challenge is managing the formation of defects such as warping, sink marks, and voids in the molded parts. Controlling the cooling rate, adjusting the injection pressure, and optimizing the mold design are essential aspects to address these issues effectively.
Additionally, ensuring proper venting within the mold cavity presents a challenge in injection molding. Inadequate venting can lead to trapped air or gases, resulting in surface imperfections or incomplete filling of the mold cavities. Maintaining proper venting is crucial for achieving high-quality plastic parts.